Building a Hydrogen-Filled Long Endurance Weather Balloon
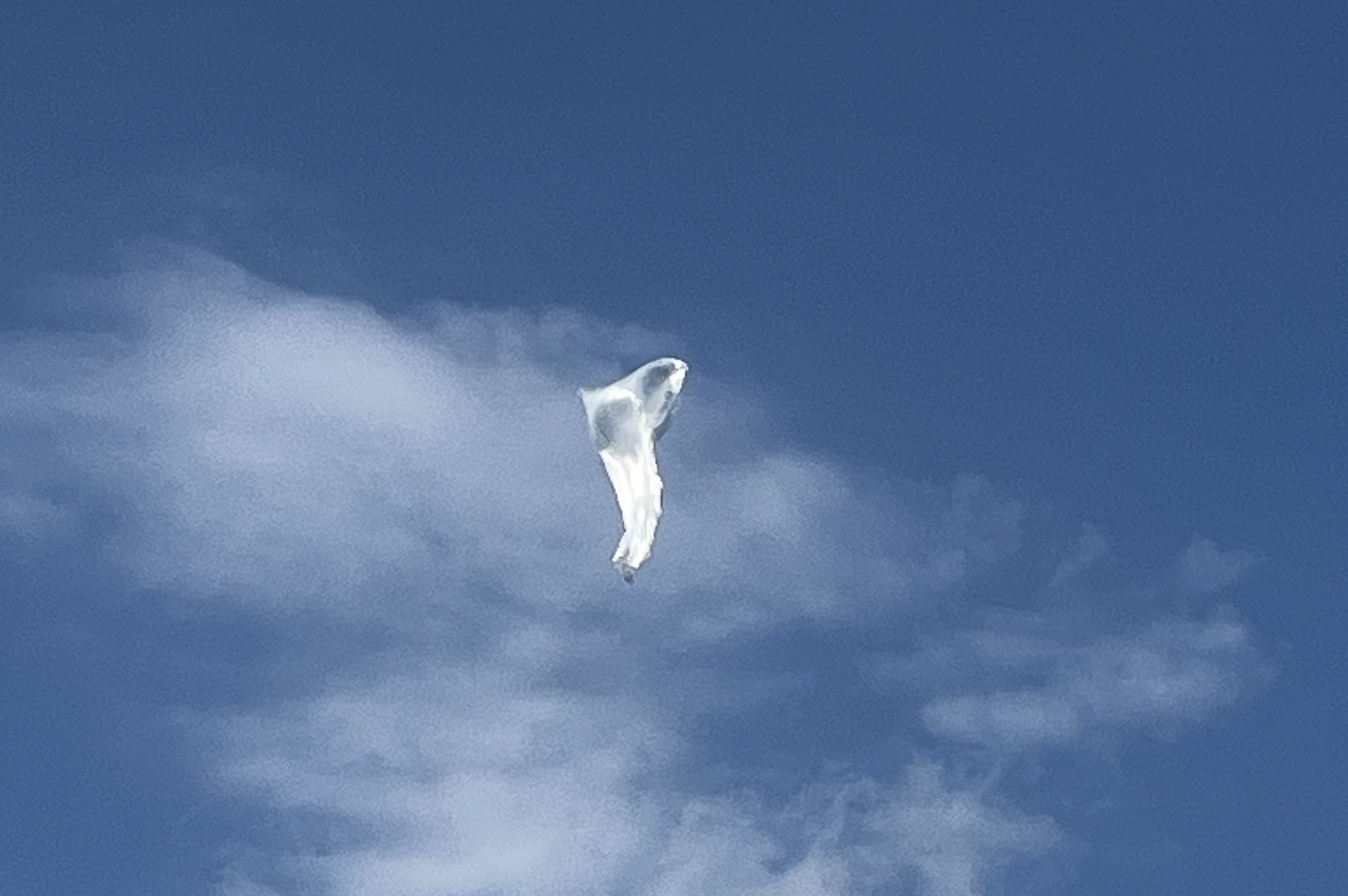
Traditional weather balloons, typically made of latex, provide only a brief snapshot of atmospheric conditions before bursting and descending. The goal here was to build a zero-pressure balloon capable of sustained vertical atmospheric profiling, extending its operational lifespan far beyond that of a standard NOAA weather balloon. Zero-pressure balloons are made from non-elastic materials with a hole at the bottom to allow hydrogen to vent out of the balloon preventing the balloon from bursting, increasing its lifespan.
Creating the Balloon Envelope
Low-density polyethylene (LDPE) was chosen for the envelope due to its lightweight properties, cost-effectiveness, and sufficient hydrogen containment. I was able to just buy extremely thin painter's drop cloth (0.31 mil) on Amazon. Early attempts focused on forming a circular mylar balloon but achieving consistent seals with a straight heat sealer was difficult. The design was simplified by opting for a "paper bag" structure—two flat rectangular sheets sealed along the edges. Though less elegant, this shape significantly eased the sealing process, resulting in a functional envelope.
Hydrogen Generation
I was building this out of my apartment so it wasn't possible to buy large pressurized canisters of hydrogen. I considered simple electrolysis but based on previous experience I knew it was difficult to properly separate the hydrogen and the oxygen that was generated from each other. I have pretty extensive experience with proton exchange membranes (PEM), but they are extremely slow. A more direct approach involved a chemical reaction using sodium hydroxide and aluminum:
2 Al + 2 NaOH + 2 H₂O → 2 NaAlO₂ + 3 H₂
Materials were sourced from local stores, including PVC for the reaction chamber and pumice stone as a high surface area distiller. The setup included an ice-cooled distillation step to condense water vapor from the hydrogen stream, as this highly exothermic reaction generates significant heat. The system’s simplicity allowed for rapid gas production, despite some complications like occasional explosions during testing, which caused hot, caustic lye to spill everywhere. Be sure to wear PPE to prevent chemical burns.
Telemetry and Data Transmission
A dual telemetry system was implemented using both APRS and WSPR protocols to transmit weather data such as humidity, temperature, and altitude, along with the balloon's battery voltage. I used a custom design that I produced on JLCPCB, however there are many open-source solutions online such as Traquito or the transmitter by Kazu AG6NS.
A lithium-polymer battery provided power for the radio electronics.
Launch
Luckily we launched on a calm and windless day. On even a slightly windy day, the breeze will try and rip the balloon apart. Launch preparations faced several challenges, especially during hydrogen generation. The cold pumice distiller setup was not effective in removing all of the water from generated hydrogen steam. Despite these difficulties, enough hydrogen was generated for a successful launch.
During launch temperatures, reached as low as -40°C causing the lithium polymer battery voltage to dramatically drop. Data was lost during this period.
Changes
Instead of using the PVC reaction chamber design to produce hydrogen gas, I developed a completely new design using an alcohol distiller and a high capacity industrial water trap. However, if you are capable of buying hydrogen gas in a canister, I would just recommend doing that instead.
Moreover, temperatures get extremely cold at higher altitudes. I would recommend putting the entire payload in a styrofoam cup and developing a heating element setup. A quick cheat is to just put a one-time-use hand warmer in there.